Structure of an underground cable system
Overhead lines can frequently been seen traversing the landscape from a long way away. This is one area in which underground cables can really score. Despite this, this transmission technology still isn’t completely invisible: above and to either side of the underground cable trench, a protective strip must be kept free of deep-rooting trees and shrubs, and no buildings are allowed to be built. What’s more, an underground cable route comprises a large number of components: the underground cables themselves, cable joints, cable transfer stations and, in the case of AC lines, reactive-power-compensation equipment. The last of the above consists mainly of reactors, which are already installed in a number of Amprion’s substations. Reactors are similar to large transformers.
We only ever switch them into the grid if the voltage on a line is too high. The reactors correct the power factor and lower the voltage on the line again. If the opposite is the case, that is, the voltage on the line is too low, correction equipment, such as capacitor banks, is put to use.
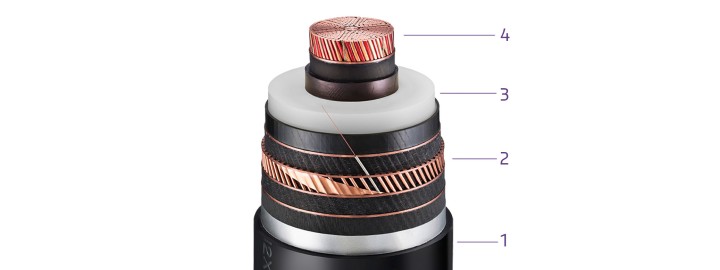
1. Cable sheath – Protects the cable, against moisture in particular
2. Wire screen – Controls the electric field and discharges fault currents
3. Insulating layer – Insulates the electric conductor
4. Electric conductor – Conducts the current
Underground cables as a transmission medium
Underground cables essentially consist of a conductor, an insulating system, a wire screen and a sheath. At the core is an electric conductor; in the case of extra-high-voltage (EHV) lines, this is usually made of copper. The conductor is enclosed by an insulating system (dielectric) whose main component is made of plastic, for example. An outer copper wire screen discharges fault currents and keeps the electric field in the cable. The outer cable sheath protects the cable against moisture.
Cable joints as connectors
Owing to the obvious transportation limitations, cross-country EHV cables can only be supplied to the respective installation locations in sections currently around 1,000 to 1,300 metres in length. Bridges and other structures impose limits on the size of the cable drums that can be transported by truck. As a result, when laying these cables, the sections have to be connected using cable joints. In order to be able to conduct electrical measurements whenever necessary, some joints allow the connections inside to be accessed from outside.
Cable transfer stations for connecting to the grid
At those locations where the cables are introduced into the ground or emerge out of it again, we build what are known as “cable transfer stations”.
These are required to connect the underground cables to the overhead lines. Such a station is very much like a small substation. Longer cable sections in the AC grid also require reactors to correct the power factor. What’s more, they require additional switchgear, which in turn takes up more space and means the transfer station as a whole requires more space.
Insulation media of underground cables
Practically all underground cables used in today’s AC grid implement a plastic insulation medium (dielectric). Thanks to the new cable joint design, which enables the joints to be prefabricated and makes them faster to install on site, as well as the better operating characteristics compared with all other types of insulation, underground cables with a plastic dielectric have succeeded in establishing themselves. The insulation material itself is usually made of polyethylene (PE) that is cross-linked in a thermochemical process to produce what’s known as XLPE. This enables the cable system to be operated at higher temperatures. However, we’re talking here about a single-layer insulation medium that has to be elaborately repaired whenever it is found to be faulty using repair joints. Plastic-insulated cable systems are available on the market for applications ranging from medium voltage right up to 500 kilovolts.
DC cable systems have a similar structure to AC cable systems, but they make much greater demands on the insulation material and on the joint technology. Many cable systems used in the
DC grid have a paper-insulated, mass-impregnated insulation (MI). With this form of insulation, a large number of layers of paper are wrapped around the copper conductor and then impregnated with an impregnating compound. This technology has been tried and tested and also offers yet another advantage: the insulating compound can rectify small faults in the insulation, rendering it to a certain degree “self-restoring”. The main disadvantage of this technology is that the cable joints are extremely complicated to install as they have to be wrapped on site. Of late, cables with plastic insulation have started to be used. Initial experiences with these are currently being gained in the voltage level up to 320 kilovolts.